更新
モノコックボディとは?特徴やメリットなど解説
モノコックボディとは?
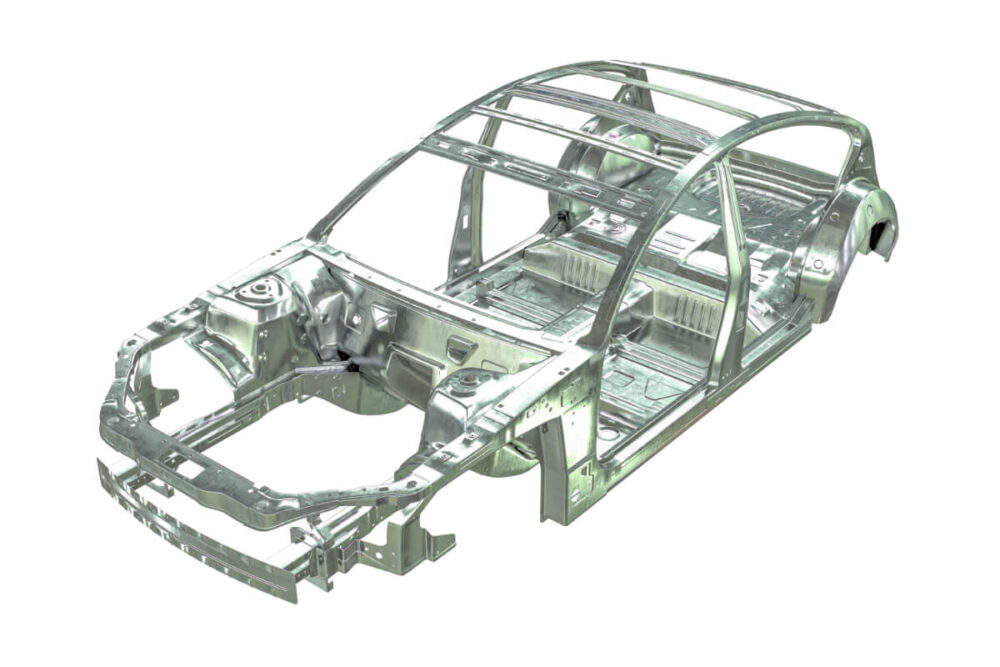
20世紀に自動車の基本性能を大きく変えたのが、「モノコック」と呼ばれるボディ構造です。モノコックによって、運動性能のみならず、燃費性能や安全性能も進化しました。
1770年にフランス人のキュニョーが世界初の蒸気自動車を造った時から、クルマはしばらく木製のハシゴ形フレームの上に乗車空間を載せたものでした。これは馬車の構造がベースにあったからです。こうした作りを「ラダーフレーム構造」と言います。
当時の製造技術が稚拙だったからということもありますが、ラダーフレームは長く使うには有利であり、同時にフレームで多様な衝撃を吸収することから、耐久性という面でも有利でした。
20世紀初頭のクルマはラダーフレームが鋼鉄製となり、これに木枠で造ったボディを載せるのがスタンダードな構造となりました。
ラダーフレーム構造からモノコック構造へ
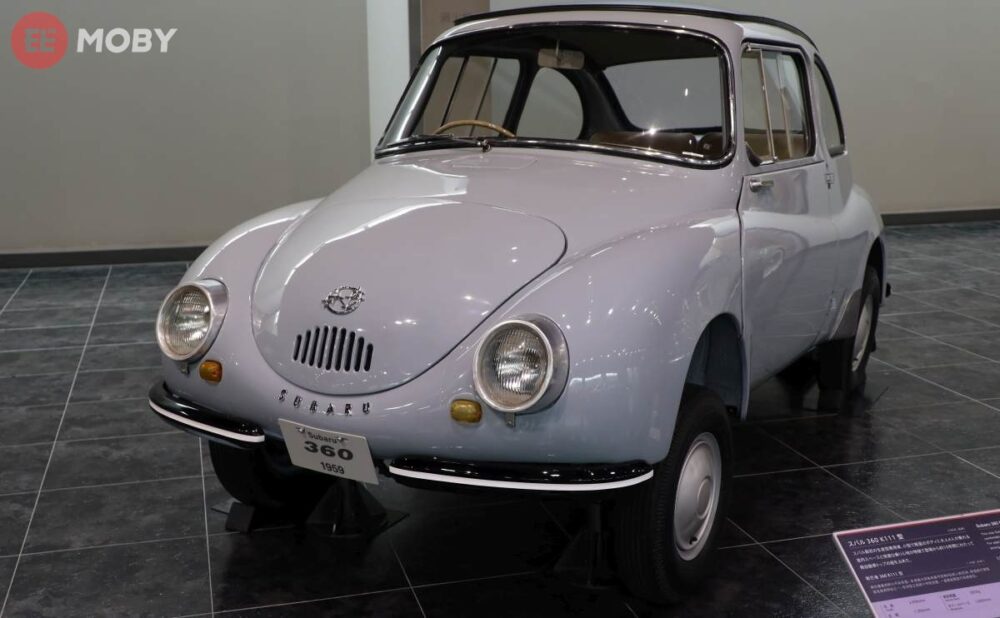
しかし、1922年に登場したランチア・ラムダは、ボディとフレームをすべて一体化した全鋼製のモノコックボディを採用。ルーフこそはありませんでしたが、フロアからサイドパネルまでが一体となっており、当時としては極めて高い剛性と軽量さ、低重心を実現していたといいます。
設計者は船の船底構造を参考にしたようですが、日本初のモノコック構造の乗用車は航空機からの技術を転用していました。それは、“てんとう虫”の愛称で知られるスバル360です。製造した富士重工(現スバル)は、元々は中島飛行機が前身で、航空機製造技術を持っていました。
スバル360はモータリゼイションでの需要を前提としたクルマであり、大量生産を考慮していました。また360ccという極めて小排気量のエンジンでも十分な走行性能を得られること、小型ながら快適な空間と安全性を確保させること、車両価格を安価にすることなどを目指した結果、航空機に使われていたモノコック構造を採用したというわけです。
ちなみに富士重工はスバル360の開発以前に、モノコック構造のバスも造っています。
ラダーフレームとは?ランクルやジムニーに使われている意図やメリットを解説
[/feed-ignore]
モノコック構造のメリットは“強度”や“作りやすさ”
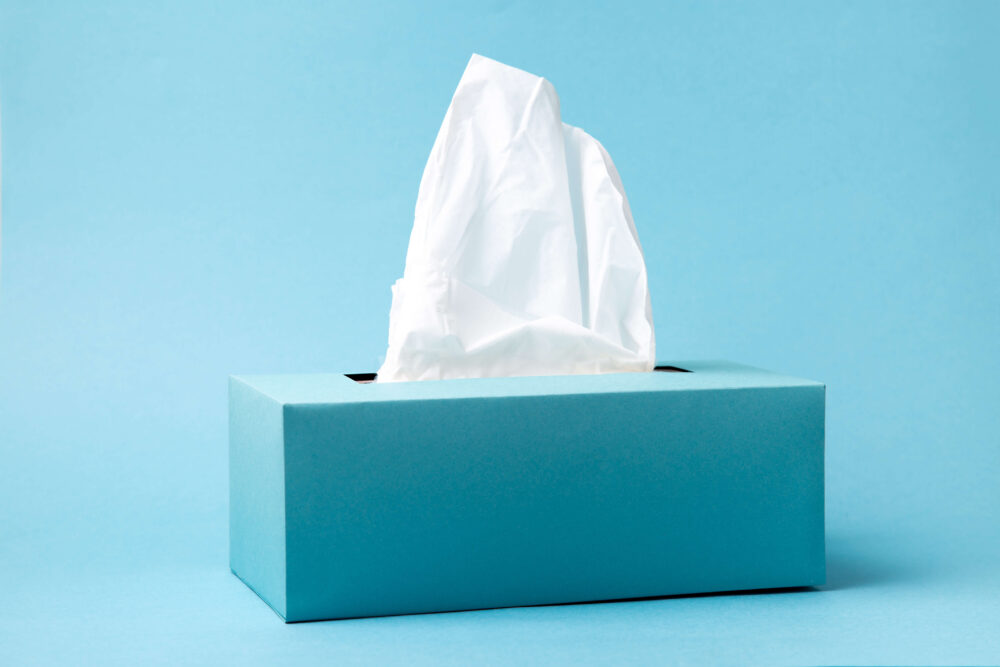
航空機のモノコック構造とは違い、クルマのそれはフレームとアッパーボディが一体化している複雑な形状です。しかし薄い鉄板を形作り、ボディの外側全体で応力を受けて分散させるという考え方は、航空機と一緒です。
モノコックボディはよく、卵の殻に例えられますが、クルマの場合はティッシュボックスの方が分かりやすいと思います。
ティッシュの箱の辺の部分を上から思い切り押してみても、なかなか潰すことができません。しかし、箱自体は紙でできており、箱をばらすと手で簡単に破ることができます。また、ティッシュの箱は丈夫なだけでなく、軽くて、作るのも簡単です。これはクルマにも言えることです。
とはいえ、クルマのモノコックボディは、一枚の鋼板から作られているわけではありません。
まず『プレス工程』によって、鋼板を金型に押しつけて、ボディの構造部品となるパーツを造ります。最近はプレス技術が進化したため、20世紀のクルマよりも複雑な形状を容易に造れるようになりました。
次にこれを『溶接工程』で繋ぎ合わせ、ボディにしていきます。最近はスポット溶接だけでなく、特殊な接着材を使用して繋ぐ車種もあります。これにより、溶接よりも軽量化できます。
出来上がったボディは塗装された後、それにエンジンやパワートレイン、サスペンションなどが取り付けられるのです。プラモデルのクルマの製作工程と似ているとも言えます。
ライバル車は羨ましい?新車販売同様にジムニーのカスタム市場が好調!理由は?
[/feed-ignore]
モノコック構造は安全性にも寄与している
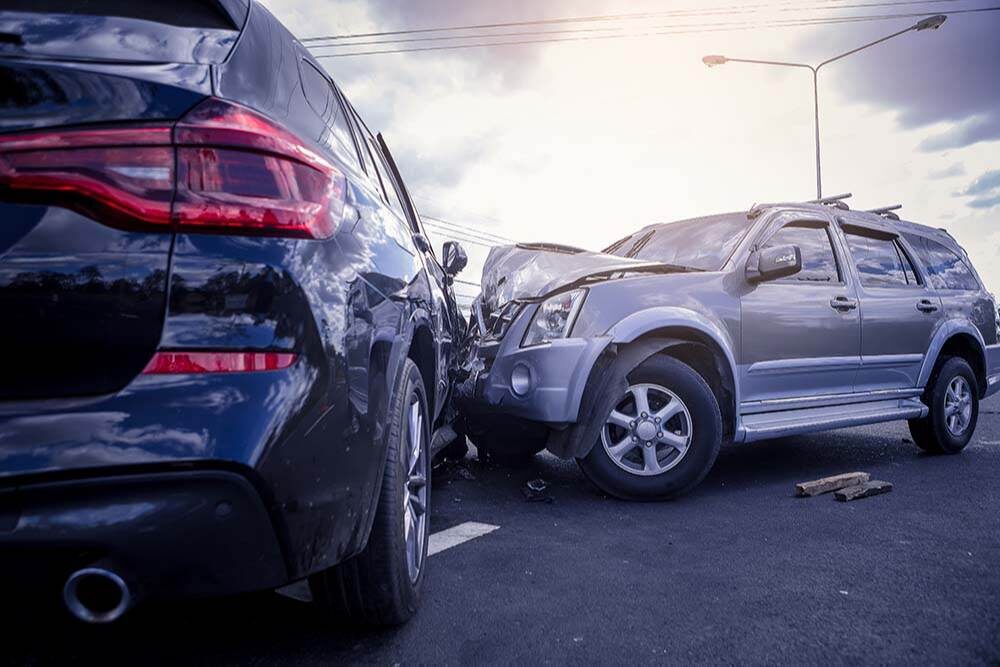
モノコック構造の美点は、製造の容易さや軽量さだけではありません。安全性という点でも、ラダーフレーム構造よりも有利なところがあります。
前述の通り、鋼板を型取って繋げていきますが、補強や部材の強度を変えることで、ボディの安全性をコントロールすることができます。これにより、クラッシャブルゾーン、つまりぶつかった時に潰れることで衝撃吸収をする部分と、セーフティゾーンという横転などをした時に強度を保持して乗員を守る部分を、設計通りに作ることができます。
ラダーフレームは強度が十分にあり、衝撃吸収性と耐久性に優れていますが、クラッシャブルゾーンの設定が難しいと言われています。
さらに、モノコックボディは、外板部分だけで衝撃吸収や強度保持は難しいので、ドアの中にサイドインパクトビームといった補強材を入れることで性能を保持させます。ドアの枚数が多いクルマは開口部面積が広いので、ボディ強度が低いように思えます。しかし、こうした補強材が入っていることから、2ドア車よりも4ドア車の方がボディ強度は高いとされています。
モノコックボディの衝突安全性は年々高まっていますが、これを支えているのがコンピュータ解析の進化です。CADなどによって画面上で衝突時の状態がシミュレーションできるようになったため、開発途中で何度も衝突安全試験を行わなくても良くなったのです。
今では乗用車の構造としてスタンダードなモノコックですが、トラックやオフロード4WDは未だにラダーフレーム構造を使っています。これは積載によって上からかかる荷重、未舗装路を走った時に路面から入ってくる衝撃を、ラダフレームが吸収してくれるからです。また、ラダーフレームとセットになるリジッドアクスル式サスペンションも、高い強度と耐久性を持っていることも理由に挙げられます。
オフロードを走ることを考慮したSUVの中には、モノコックボディに補強材を入れ、お互いのメリットを補完した「フレームインモノコック」という構造を採用している車種もあります。
このように、ボディ構造はそのクルマに求められる性能や条件によって、採用されるものが変えられるのです。
軽自動車もSUVも重くなっている理由は?
大阪生まれの、シュッとしたイタリアン大衆車
- 執筆者プロフィール
- 山崎 友貴
- 1966年生まれ。四輪駆動車専門誌やRV雑誌編集部を経て、編集ブロダクションを設立。現在はSUV生活研究家として、SUVやキャンピングカーを使った新たなアウトドアライフや車中泊ライフなどを探求中。現在の愛車は...